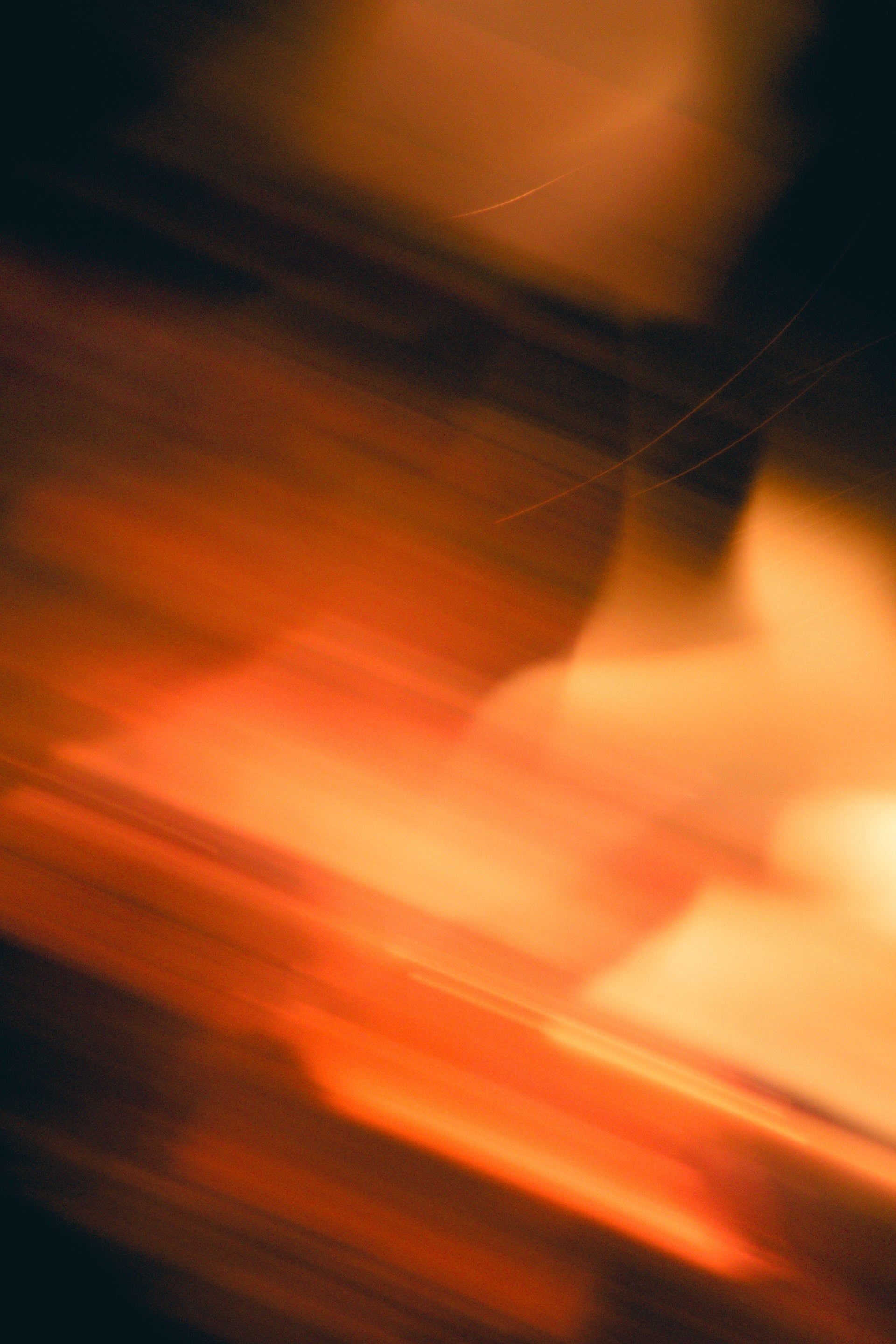
test team leader
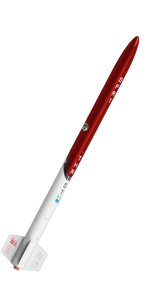
The Thrust Team
The THRUST Student Project was born out of a desire to fill a gap in hands-on rocketry experience at the University of Padova. Recognizing the absence of a dedicated student rocketry team, I took the initiative to establish one. I reached out to the professor of aerospace propulsion and successfully secured university support and funding to launch the project. What started as a passion-driven endeavour quickly grew into an award-winning team designing and manufacturing a hybrid-propelled sounding rocket. As a co-founder and leader of the testing sub-team, I played a key role in developing the test stand, designing a gas cylinder rotator, creating P&IDs, and developing test procedures.
The team's goal is to participate in the European Rocketry competition in Portugal, EUROC | EUROPEAN ROCKETRY CHALLENGE.
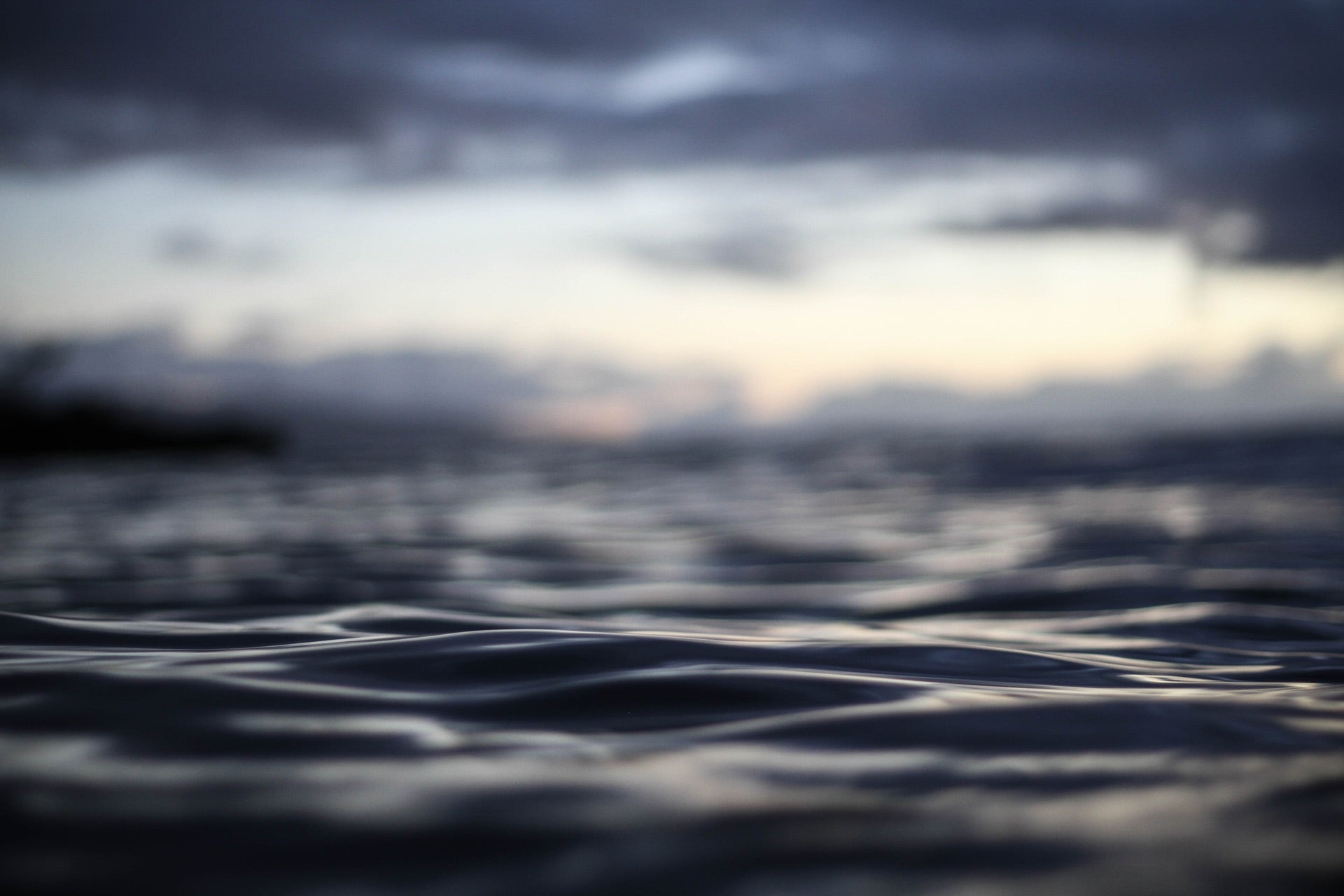
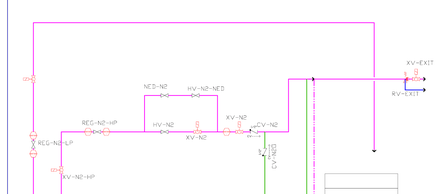
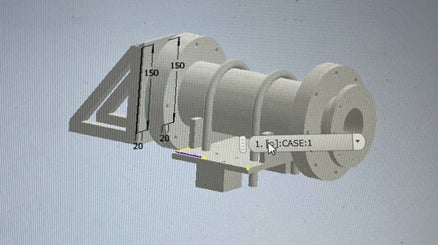
Test Stand and P&ID
We inherited T4i's old test facilities which had to renovated and adapted to our setup.
Fluidic lines to supply the test stand with N2O, N2, and water had to be installed. We designed the P&IDs and we assembled the entire fluidic system.
There were several different ideas on how to design the Engine stand and we ultimately decided on the one seen below.
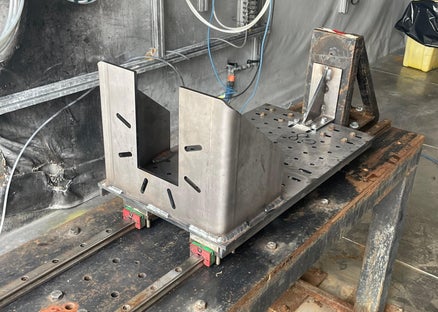
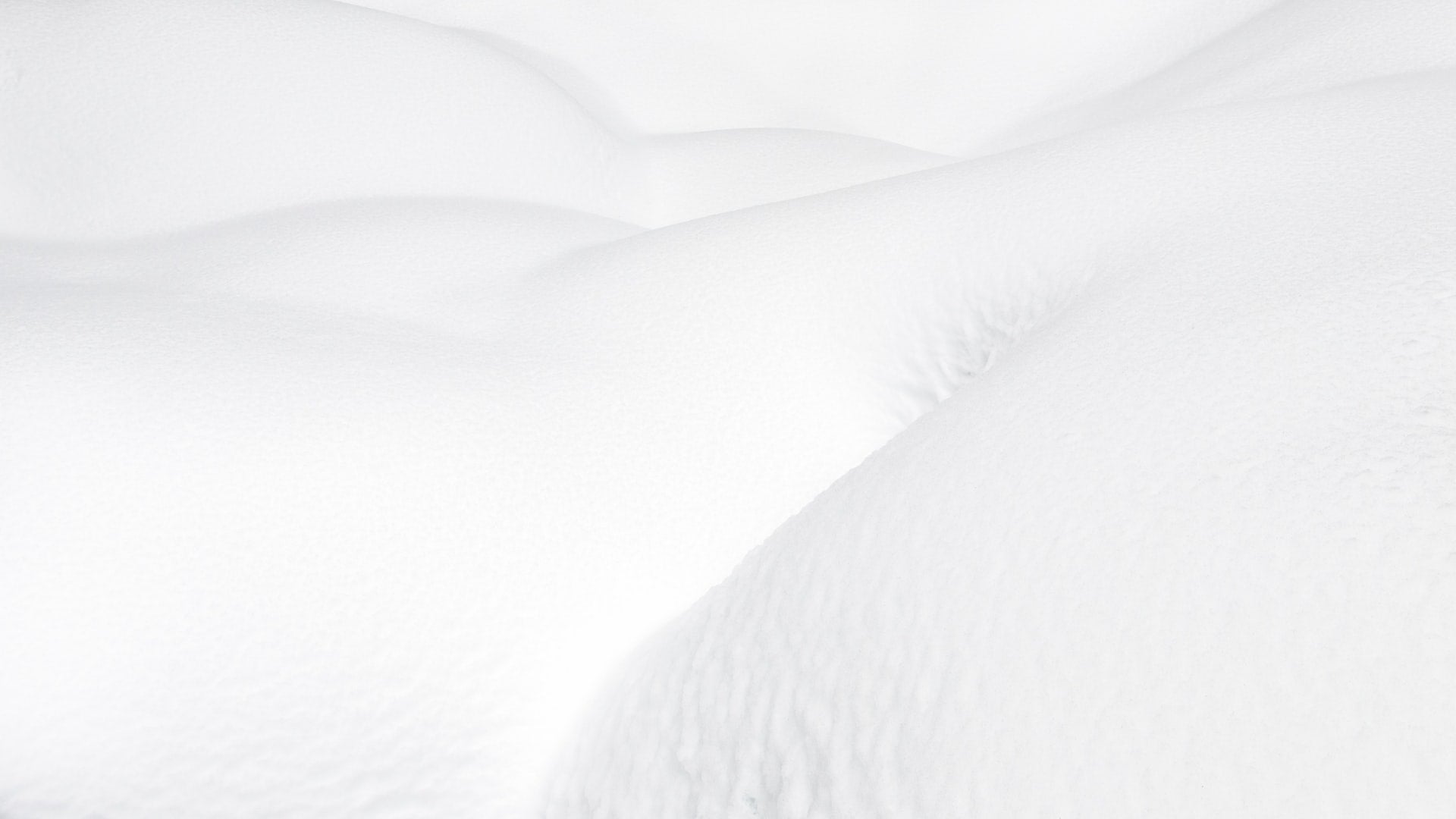
MAIN VALVE
The valve I helped design served as the main interface between the oxidizer tank and the combustion chamber, playing a crucial role in the hybrid rocket propulsion system. It was a pressure- and spring-activated mechanism, designed to open and close in response to combustion chamber conditions. When the chamber pressure increased, it acted on the lower section of the piston, lifting it and allowing propellant flow. Once the pressure dropped below a critical threshold, a spring mounted around the piston forced it back into the closed position, effectively shutting off the flow. This self-regulating design ensured reliable and responsive operation without requiring external actuation, enhancing both system simplicity and performance.
The valve had different ports:
1. Filling port which used a check valve. (right side in image)
2. Abort port: could be activated to use some of the tank pressure to push the piston form above and close the valve.
3. Pressure release port which used a rupture disk.
4. A port (in the lower part of the valve) which would be screwed onto the combustion chamber.
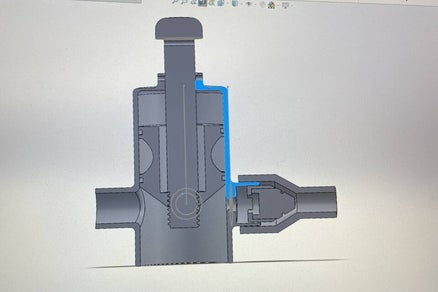
Public speaking
I was honored to represent the team, and give a pitch at the Veneto at the Space Meetings Veneto
While I was part of the team, THRUST expanded into a 58-member team and gained recognition at Italian Space Day 2022 as the most innovative project.
Tank Support for Test Stand
In order to know the weight of the tank during a test, I developed a special setup to be able to place a Load cell underneath the tank. We took some cool pictures to post on Instagram
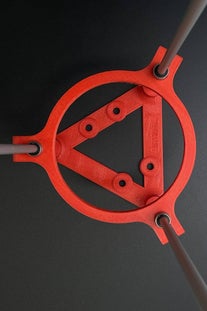
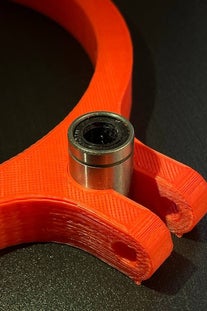
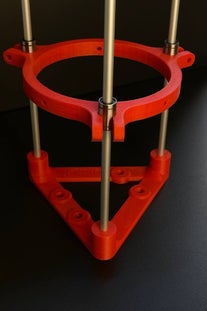
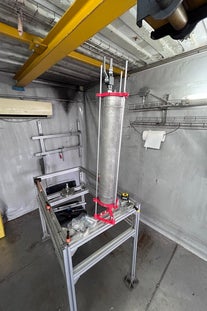
Images from Thrust
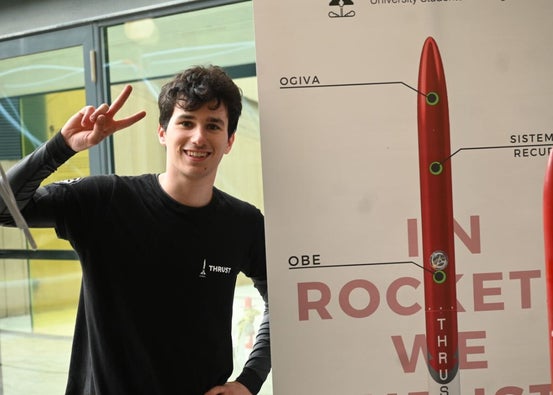
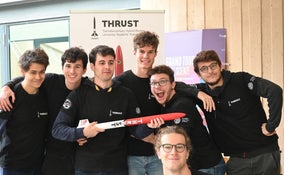
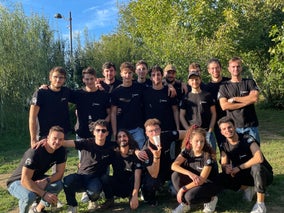
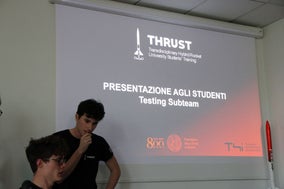